A bright future for modular drainage and water supply systems
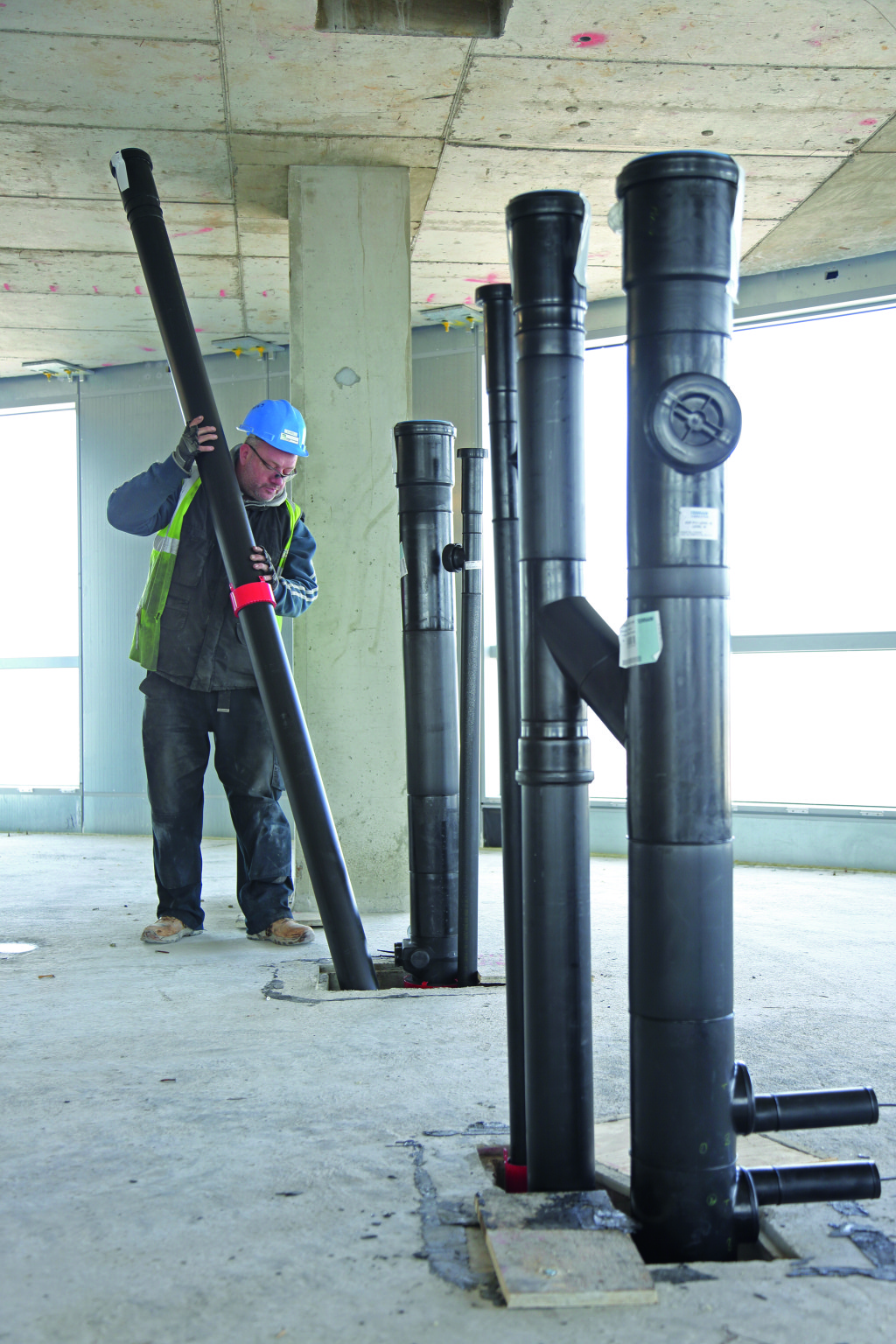
Adam Cafer, Advantage Manager at Polypipe Building Services, discusses how projects are realising greater benefits from working with suppliers who are focussing on modern methods of construction.
Modular construction is growing in popularity within the UK. Whilst other European countries have used modern methods of construction (MMC) widely for some years, here it has suffered from a prefab, post-war image, which it’s struggled to throw off since the middle of the last century.
But high-profile projects making good use of MMC plus an increasing use in other commercial sectors such as hotels, has served to highlight the benefits to be gained across many different types of buildings. Significantly, the government recognises the value of MMC and through bodies such as Homes England have made it a strategic priority.
Maximum benefit
As MMC projects grow in popularity, work is needed behind the scenes across different building services disciplines to identify exactly how these techniques can offer maximum benefit both to those involved in construction and those using the finished buildings. Here at Polypipe Building Services we have been exploring the potential benefits specifically for drainage and water supply systems.
Though there have been upgrades to both worker safety and materials, the method of delivering commercial construction projects has pretty much remained the same since the 1960s. MMC promises to rectify this by applying more sophisticated techniques. Of the various methods that fall under the MMC moniker, the use of offsite construction is one that we have focussed on in particular – and in relation to how this supports more efficient modular projects.
Solving design issues
Offsite construction allows significant portions of what would otherwise be site-based work to be performed in a controlled environment and, depending on project needs, on a near assembly-line basis. Offsite manufacturing has been a specialist service supplied by manufacturers for some time because it simply solves design issues and allows products to undergo robust testing before they get to site, reducing risks of costly mistakes.
We anticipate offsite fabrication to be one of the fastest growing areas for us in the next couple of years. Offsite construction is a proven approach to help solve many challenges the construction industry is facing, such as labour shortages, rising material costs, changes in building regulations and the push towards net zero. These factors combined are all fundamentally driving new approaches to construction.
Key to this is for manufacturers to ensure they have the technical capabilities in-house to allow for full offsite fabrication of systems to meet the specifications of different projects. The primary benefit of doing this is time saving – as both drainage and supply systems traditionally demand time on-site to undertake the likes of welding and jointing, not to mention cutting standard pipe lengths to size. Instead of needing installers to do this work on-site, potentially holding up other trades, much of this work can be completed in the controlled environment of a factory.
Pre-testing systems
Another advantage to this process is that testing of the entire system can be carried out before it is shipped – meaning installers can be confident they are receiving a fully air tested system. This can then either be taken directly to site or to the facilities of the modular construction company who are able to quickly install the systems into, for example; bathroom or kitchen pods with minimal work and testing required. We have found materials such as high-density polyethylene (HDPE) are ideal for this purpose as it offers a greater level of versatility than traditional materials when it comes to offsite construction and allows us greater flexibility to adapt and create designs to address specific customer challenges.
The alternative to this would not only demand more time spent on site, potentially impacting the schedules of other trades, but also result in much higher levels of waste as standard pipe lengths are cut to fit. Where waste is created, whether on-site or in a factory, materials such as HDPE are 100% recyclable. This means that any excess product from the production process can be reused, whilst at the end of a buildings’ life – however long that may be – during the deconstruction phase the drainage system can be recovered and reprocessed or recycled and used to manufacture further products.
Recognising the benefits
We have supplied bespoke off-site fabricated products for a range of different commercial applications, including healthcare, education, multi occupancy residential, commercial high and mid-rise, student apartments and hotels. All have recognised the benefits in terms of efficiency and quality assurance, as well as health and safety from minimising the need for work on-site.
One of the challenges that can be faced – and one that will be important to overcome as MMC projects become more widespread – is to ensure early engagement on projects for more effective collaboration with specifiers and contractors to shape a solution that fits a specific project demands.
Flagship project
For us, if we understand the site and their building requirements, we can understand their specific challenges and meet them. Another example; a flagship project in Manchester the customer wanted fabricated stacks that they were to install in bathroom pods before they were delivered to site. Because we were involved early in the process, we were able to produce an example drainage stack in the required dimensions which they could take to their pod manufacturer to make sure it was the right fit. With about 20-bathroom pods per floor, this meant significant time savings, if these were done the traditional way it could have taken a week to install. This type of install meant an entire floor can be connected in about half a day.
What the market wants
We have found that the market is interested in two methods of meeting this demand. Full design and fabrication capabilities which allows contractors to make progress with a made to measure drainage or supply system that can be efficiently installed on-site or as part of modular pods. Alongside these fabricated systems designed to meet the most common applications for kitchens, utility rooms and bathrooms in commercial buildings. So, whilst this is not bespoke to an individual project, it increases efficiency for repetitive work where otherwise each room would need cutting and jointing.
It's exciting that we are still in the relatively early stages of realising the benefits of MMC, and there will be even greater benefits to come as these techniques mature and become commonplace. The key will be to continue collaborating across projects to find the best solutions that fit the needs of each particular building.