Designing out pumping costs

Are the pumps in your heating or chilled-water system using anything up to five times more energy than they need to? Dr Arnold Teekaram outlines how to design systems that are inherently more efficient.
In building-services applications, heating and cooling systems usually incur the largest pumping loads, and the potential for reducing pump energy consumption is substantial.
The US Department of Energy estimates that pumping accounts for 20% of the world’s energy use by electric motors. Europump (a pan-European association of pump manufacturers) estimates that systems could be 30 to 50% more energy efficient by careful consideration of components, design and installation.
BSRIA’s recently published design guide BG12/2011: Energy efficient pumping systems’ shows some ways in which this efficiency may be achieved. The guide is a result of research project undertaken by BSRIA with the support of BRE Trust and a steering group drawn from the following companies: Andrew Reid & Partners; Belimo Automation UK; Crane Fluid Systems; Danfoss Randall UK; Frese; Grundfos; Herz Valves UK and SAV UK.
The recommendations presented here are based on analyses of alternative pipe-sizing methods, pipework layouts, valve selections, pump-control options and system-control measures. Separate research reports for each recommendation are also available from BSRIA.
Most of the findings are applicable to both heating and cooling applications. Some are specifically for heating systems, including district heating, because a lack of regard for pump energy may lead to missed energy savings elsewhere. For example, excess flows tend to reduce system temperature differentials, thereby reducing the effectiveness of some low-carbon or renewable-energy heat sources.
Energy is frequently wasted in pumping systems, and this wastage can be significant. There is a potential difference of 80% in energy consumption between the worst designed constant-flow systems and the best designed variable-flow systems.
A pumping system capable of realising this energy saving will have the following properties.
• It should be a variable-flow system with a pump that varies its speed to match the operating load conditions.
• Pump speed should be controlled so as to maintain a constant pressure across the most remote pressure-controlled sub-branches.
• Design flow rates should be minimised by maximising system design temperature differentials.
• Pipes should usually be sized as large as possible, allowing for practical considerations, to minimise resistance.
• Pressure losses through pipe fittings should be minimised by avoiding bends or using wide-swept bends wherever possible.
• The system should incorporate some means of automatically controlling differential pressures, and hence flow rates, across all terminal unit branches .
The best options are the following.
• Pressure-independent control valves (PICVs)s in terminal unit branches.
• Differential-pressure control valves (DPCVs) in valve modules serving two to eight terminal unit branches.
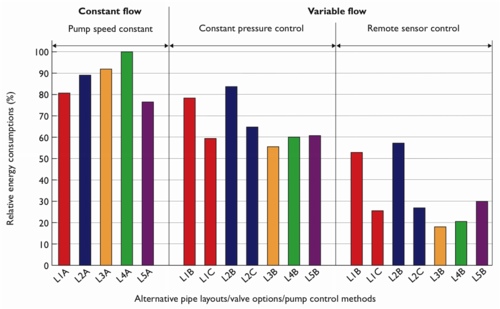
• DPCVs on radiator sub-branches where the pressure controlled constant by the DPCV is not greater than 10 kPa
• DPCVs on heating/cooling coil sub-branches where the constant pressure that is controlled by the DPCV is not greater than 1.5 times the design pressure loss across the end terminal unit branch with the largest design pressure drop.
• Reverse-return circuits using a differential-pressure sensor to maintain a constant pressure across terminal unit branches.
To achieve the best performance from a heating or cooling pipework system, the system temperature differential must be maximised under all operating conditions; the following guidelines can be used.
• The system can be either constant- or variable-temperature depending on the application, since pump energy issues would be secondary to the control of heat output.
• The system should be variable flow in order to maintain temperature differentials at part load.
• System bypasses should be designed such that the bypassing water is part of the system water rather than in addition to the system water.
• The amount of water bypassing the terminal units and heat-exchange devices should be minimised — the minimum being that which can be managed by the pump without causing unacceptable heat gains to flow water.
• The system should incorporate some means of automatically controlling differential pressures and, hence, flow rates across all terminal-unit branches.
• Circuits serving hot-water heaters should be designed to maximise temperature differential. This is best done using a high-performance heat exchanger such as a plate heat exchanger.
• Primary circuits should be designed so that their flow is variable and matches, as closely as possible, the sum of flow rates through secondary circuits.
• Primary circuits incorporating heat sources with low carbon emissions should be designed so that the low-carbon heat source gets priority over other conventional heat sources and is permitted to run for the maximum possible duration.
As the bar charts (Fig. 1) show for five pipework layouts (note the five colours), being able to vary the flow reduces pump energy consumption compared with constant flow. Pipe layouts remain the same, and the reduction in energy consumption is due to the use of various combinations of control valves and sensors. Note how the two types of reverse-return layout (yellow and green) have the highest pump energy consumption with a constant-speed pump but the lowest (about 80% less) with a suitably sized variable-speed pump and the best use of control devices and sensors.
Further guidance on how to realise the cost-saving and operational benefits of energy-efficient pumping systems is available from the BSRIA Guide BG12/2011, which can be purchased from the BSRIA Bookshop.
Dr Arnold Teekaram is head of test and certification with BSRIA.
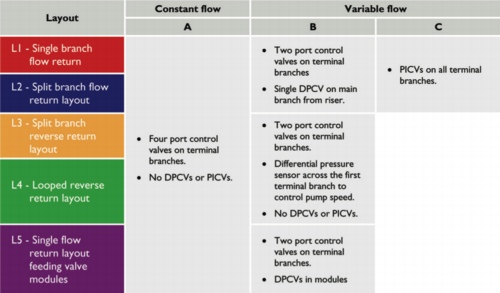